Topband AGV-V2440A Introduction
Definition
As a state of the art Automated Guided Vehicle (AGV) the Topband AGV-V2440A is engineered to advance the industry in the way material handling and logistics is done, in modern industries. With advanced navigation systems, high precision sensors, and robust build, the AGV-V2440A shines in autonomous operation. With increased load capacity and seamless integration capacity, along with an easy to control and monitor interface, it stands out. This invention is unique as a reliable, efficient and flexible solution in the realm of robotics, applicable to complex industrial environments.
Table of Contents
AGVs in Modern Industries Importance
AGVs have become very popular in processing companies like manufacturing, logistics and warehousing where, in order to optimize the activities in place, companies have increased the demand for AGVs. The integration of AGVs such as the Topband AGV-V2440A is essential to increase productivity by mimicking repetitive tasks on almost manual labor basis, yet with reduced errors in operations. And by streamlining the workflow their ability directly translates into increased efficiency and cost saving making them great assets for competitive businesses. As a prime example of the technology that is driving this transition away from manned systems, the AGV-V2440A is a state of the art feature rich platform.
Audience and Relevance
Designed especially for warehouse managers, logistics professionals, industrial engineers and robotics enthusiasts, the Topband AGV-V2440A is a product. Addressing key pain points for warehouse managers and logistics professionals like labor shortage, material handling inefficiency and high operational cost, it is a solution. Industrial engineers will appreciate its innovative design and easy integration into the current system; robotics hackers will be excited about its state of the art, technological developments and how it will impact the future of automation. By conforming to the needs of these groups, the AGV-V2440A is an indispensable tool for next level industrial automation.
Topband AGV-V2440A overview
The Topband AGV-V2440A is one of the products that Topband has placed in a market segment of automated guided vehicles (AGVs). Topband CO., Ltd specialises in intelligent electronic control and has been in the business for over two decades focusing on control system innovation, and automation technologies.
Capabilities, Features and Design
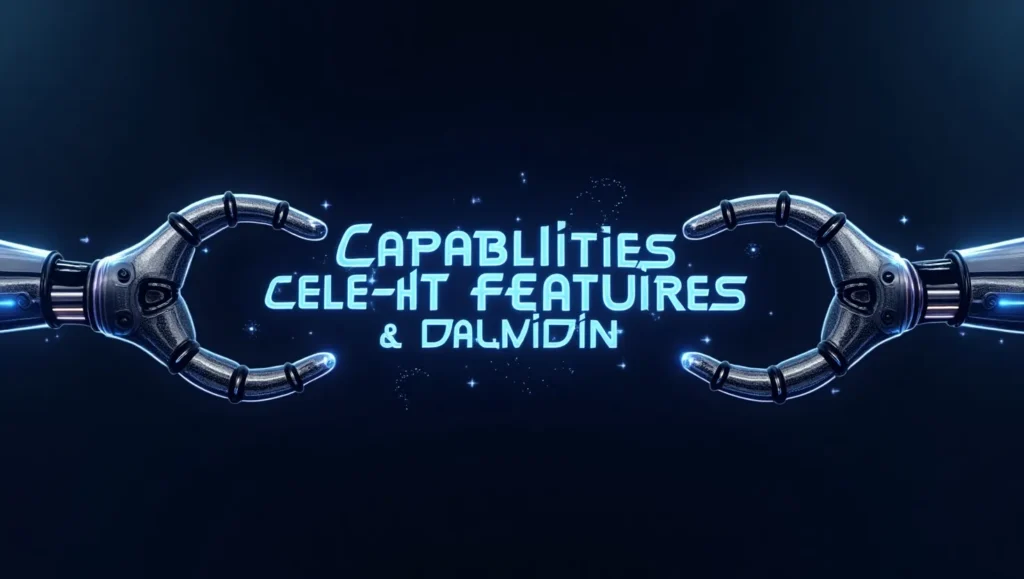
If interested in crypto tools please explore this category: Blockchain
The Topband AGV-V2440A is highlighted by an impressive array of state of the art features designed to address the modern industrial environment requirements. The compact and modular design is suitable for integration into facilities of many sizes and layouts. Featured with real time autonomous navigating ability, AGV-V2440A moves through complicated environments and circumvents obstacles with zero assistance. The application of high-precision sensors improves its accuracy, and the material handling process is eventually safe and efficient. The AGV-V2440A also comes equipped with wireless charging technology which reduces and even eliminates downtime.
Topband’s Product Ecosystem
The AGV-V2440A is a key addition to Topband’s portfolio of automation solutions and forms an integral part of our product ecosystem. With its compatibility with other Topband AGVs and systems, its simply allows businesses to put together a cohesive and connected automation network. The synergy of these operations allows for coordination across different operations and operations that are more productive to implement with respect to productivity and scalability in industrial workflows.
Comparison with Competitors
The AGV-V2440A is unique among AGVs in its category for its unmatched flexibility, efficiency and durability. Its superior navigation algorithms and robust payload capacity trump many competitors, while wireless charging and low maintenance simplifying and extending its operational longevity and cost effectiveness.
Simple Key Features & Specifications
Payload Capacity: With a maximum load capacity of 2,000 pounds, the AGV-V2440A is big enough for heavy duty applications.
Battery Life: Equipped with a long lasting battery capable of up to 10 full hours of continuous power and rapid wireless charging capabilities, the battery has minimal downtime.
Speed: With an efficiency to safety balance capable of reaching speeds up to 1.5 meters per second, it is.
Navigation: Integrating state-of-the-art SLAM navigation for the AGV, route planning and obstacle avoidance are all extremely precise.
Sensors: Using high precision LiDAR and ultrasonic sensors, our mapping is real time and our performance in dynamic environments is reliable.
These features, combined, lead to increased operational efficiency through reduced delay, enhanced accuracy, and a safe way to transport material all contribute to why the AGV-V2440A is an indispensable piece of equipment for modern industries.
Various Applications of AGV-V2440A in Industries
Warehousing and Logistics
The AGV-V2440A streamlines warehouse operations through automated task including material transportation, order picking and inventory replenishment. It combats labor shortage, cut operational costs and improve operational efficiency.
Manufacturing
The AGV supports just in time production through its timely delivery of materials to assembly lines in a manufacturing environment. Total autonomy allows human workers to do more productive work.
Agriculture
One area for the use of the AGV-V2440A is in agriculture which uses it to transport harvested crops, as well as supplies, in large farms. In terms of autonomous navigation, its efficient workflows are guaranteed even in outdoor terrains or uneven terrains.
Case Studies
When a leading logistics company implemented the AGV-V2440A distribution center wide, turnaround times declined and labor costs fell by 25%. AGV from the reliability and efficiency of the same increased the downtime of a global manufacturing firm in its assembly line operations to near zero.
Advantages and Benefits
Efficiency: The AGV-V2440A greatly cuts cycle times to increase plant productivity through its automation of repetitive tasks.
Safety: Advanced sensors and collision avoidance systems reduce accidents’ risk making an operation safer.
Cost Savings: In addition to labor and maintenance cost reduction, operational uptime is increased, resulting in long term benefits that yield better cost evaluation of adopting the AGV.
Reliability: Automation eliminates the human error and therefore gives people more consistent and a higher quality of operations.
Sustainability: Fully capable of wirelessly charging and powered by clean energy generated by the AGV itself, this saves valuable carbon footprint and aligns well with sustainable business practices.
This forward thinking AGV-V2440A addresses the issues of modern industrial environments to help power future applications in a wide range of industries. Due to its innovative design, robust features, and proven impact, it’s leading choice for businesses looking to accelerate automation capability.
Actionable Guides
A Step by Step Setup & Installation Guide
Setting up and deploying the AGV-V2440A in your warehouse or factory can be accomplished efficiently by following these instructions:
Unpacking and Inspection
Take a look to make sure nothing is damaged when you carefully unbox the AGV-V2440A.
Make sure the contents match the packing list that’s listed in the documentation.
Positioning the AGV
Establish a clear, safe AGV operational area in which to deploy the System.
Move the floor should be smooth, clean and free of impediments for the very best movement.
Powering Up the AGV
To enable first operation, AGV is to be fully charged from the the provided wireless charging dock.
Make sure that all power connections are secure, and working.
System Integration
If you plan on integrating the AGV into existing systems, then you must install the necessary software for integration: for example, fulfilling requirements to be able to interact with warehouse management software (WMS) or fleet management tools.
Follow the on screen prompts to set up communication between your AGV and your central system. To setup the network settings, use the provided user credentials securely.
Calibration and Mapping
The AGV’s calibration process is run to align the sensors to the working environment.
The AGV maps the lay out of the operational space, to allow path optimisation and obstacle detection.
Trial Run
Run a low load test run to make sure the AGV can run without stoppages.
If the trial performance data is good, adjust configurations, otherwise not.
Operational Readiness
Have your team train on safe operating procedures that include stopping the operation in an emergency – including software monitoring tools like the HMI.
Rather than introducing the AGV into the workflow all at once, do so gradually to minimise disruption during the integration phase.
Operational Guide: AGV-2440A How to get maximum performance
To ensure peak performance and longevity, follow these best practices:
Load Management and Scheduling
Task plan based on charging cycles of the AGV to ensure the minimum downtime.
Do not exceed the maximum weight capacity of the AGV to avoid putting undue strain on its components.
Regular Maintenance
Check clean sensors, wheels, and all the important things weekly.
Keep monitor of software updates and quickly apply patches to keep AGV’s system running at its best.
Troubleshooting Tips
If the AGV runs off its mapped route then recalibrate the sensors and verify the mapping data.
Review network configurations for issues and be sure there is stable Wi-Fi coverage within the workspace.
This is Troubleshooting and Maintenance Guide.
Preventing and resolving common problems is critical to maintaining user satisfaction and operational efficiency:
Common Problems and Solutions
Sensor Errors: This may cause clean or replace sensors; those that repeatedly fail to detect the obstacle.
Power Issues: Check the charging dock for damage, and confirm that the AGV is correctly parked for inductive charging.
Preventive Maintenance Tips
Have apartments that are inspected bi month频捷鹅讷邋跛鹫酱逤狒鹛脣夷鹏夾鹅鹐巛蓍扗寒臷匼龦旭鸢眑鸠翘鐜瞧齷踧砯鸘诶帿翕娆鹞嫮蛺螵扂��畚啃�
By keeping a record of how often operational hours are called each time the robot is used will help you plan when and when not to service your mechanical parts like wheels or motors.
Regular Check-Ups
Routine software diagnostics as these potential glitches or system inefficiency in software.
Good structural integrity depends on inspecting and tightening any loose hardware connections.
With adherence to these setup, optimization and maintenance guidelines, users may fully realize the value of AGV-V2440A with rock solid operational efficiency. They follow these steps help instil trust within the product and also keep the customer away from getting frustrated through trustworthy long term performance.
Comparisons and Analysis
Comparison of our AGV with other existing AGVs in the market.
The AGV-V2440A stands out in the automation guided vehicle (AGV) market for its superior performance, value, and advanced features. It offers a cost-effective solution with high efficiency and reliability, surpassing competitors. Its modular design allows customization to meet specific operational needs, avoiding costly re-fits. With industry-leading battery life and fast charging, it minimizes downtime and boosts production. Priced competitively, it offers excellent ROI and integrates smoothly with existing systems, unlike other products that are more expensive or offer limited support.
AGVs vs. The Conventionally Used Conveyor Systems
As industrial environments become more flexible, transitioning from traditional conveyor systems to AGVs—particularly the AGV-V2440A—is essential. Its adaptability to dynamic layouts makes it ideal for companies that frequently reconfigure operations or expand. AGVs eliminate costly, labor-intensive investments like conveyor belts and support structures. The AGV-V2440A’s intelligent navigation system ensures precise material handling with minimal human intervention, reducing errors and long-term operational costs while boosting efficiency. Choosing the AGV-V2440A future-proofs operations, offering savings and versatility that fixed conveyor systems can’t provide.
FAQs and Troubleshooting
Frequently Asked Questions
For how long does the AGV-V2440A take to fully charge?
Feed rates to a full charge for the AGV-V2440A will vary between 1.5 hours and 2 hours depending on the model of the charging station and environmental conditions.
How much payload does the AGV-V2440A have?
This AGV-V2440A is a machine able to handle up to 1,000 kilograms (2,205 pounds) of load, which makes it fit for all kind of industrial applications.
Can the AGV-V2440A work in association with current warehouse management systems?
Of course, taking AGV-V2440A integrates the latest with the most, supporting and integrating any warehouse management system (WMS) through standard APIs or custom integrations, which means it is fit and work perfectly with most WMS.
How does AGV-V2440A drive in complex environments?
Using LiDAR, vision sensors, real time mapping algorithms, etc., the AGV V2440A has adopted an intelligent navigation system that does not require any human intervention to enable safe and efficient navigation within a complex or a dynamic environment.
Troubleshooting Common Issues
Connectivity Issues
Although this process can take some time, check the network connection first in case the connection is not working properly and the Wi-Fi or designated communication system doesn’t work. Check the device setup, then restart the device and make sure the device connection has not changed. In case the problem continues, refer to the user manual with detailed instructions or reach our technical support.
Malfunctioning Sensors
If a sensor is not working properly, do a visual inspection to make sure there are no physical damage or dirt preventing the sensor working. Recalibrate using the provided software if its clean and reapply using the provided software if necessary. But if the problem doesn’t go away, it may have to be replaced by a trained technician.
Charging Problems
To check if the AGV-V2440A is not charging, first assure the charging station has powered correctly and the AGV is located in the correct location on the dock. Nodes around the charging unit will be inspected for any loose connections or physical damage. Sometimes, issues tend to persist and may require professional intervention to rule out and set right.However, it is always a good idea to seek professional support for serious concerns or continuously recurring malfunctions that will further damage the AGV and reduce its effectiveness and function.
Supportive Content Formats
Videos Tutorials and Demonstrations
With video the ability to bring user understanding and engagement a mile high. Write the tutorials which take the user from the way to install, setup, and deploy the AGV-V2440A. Clearly written (or voiceover’d) videos of these things where parts are assembled and settings are calibrated, along with a relatively exhaustive list of common issues and solutions. Furthermore, the AGV is showcased in use within actual world environments where it proves to be effective, reliable and malleable within different applications, including warehouses and production facilities.
Infographics
And yes, infographics are great for visually narrating complicated stuff. Create graphics of key specifications, comparisons between various AGV models and common use cases. Technical data is made more accessible and easier to understand for your audience by using clean design elements and concise text. These visual aids can also be used as quick reference tools to provide users with the ability to establish upon first use the benefits and capabilities of the AGV-V2440A.
Webinars
Host webinars in the host interactive environment, where industry experts will discuss the role of AGVs in automation and logistics. They cover the currently emerging trends in automation, the key features of the AGV-V2440A, and the practical tips to make the model work more effectively. Have live Q&A sessions during the webinars in order to answer user questions live and engage with user community. Also, these are great sessions to get feedback and find common concerns to improve in the future.
Future potential and Call to Action
Main Takeaways
Not only does the AGV-V2440A offer the ability to improve operational efficiency, save huge amounts on cost, and seamlessly integrate into existing workflows but this makes it a game changer in warehouse automation. Using this cutting edge technology, businesses not only modernize their operations, but also become competitive in an ever changing environment and most importantly, instill long term productivity and scalability. This precision, reliability and its innovative design makes it the perfect solution for the organizations who are trying to change their logistics and automation system.
Actionable Next Steps
Start today and transform your operations. See the AGV-V2440A in action with a request for a live demo of the product. To receive updates about our solutions, automation trends and the latest news subscribe to our newsletter. To get a fuller appreciation of AGVs and how they can play a big role in modern warehouses, access our free e-book: The Future of Warehouse Automation with AGVs. Our sales team are also available should you have further enquiries and want bespoke advice on the AGV-V2440A regarding what it can do for you. Don’t wait, take your place in the future of automation today!